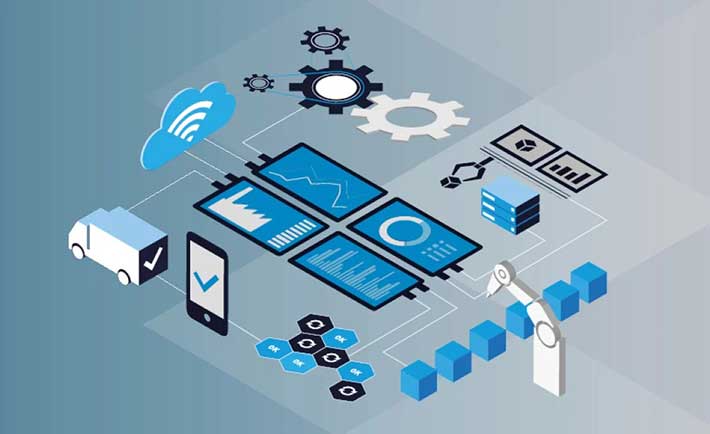
La TI industrial ha experimentado muchos cambios durante la última década, con la convergencia de TI / OT, Industria 4.0 y una mayor digitalización, todo ello dando forma en cómo la planta de producción se conecta e interactúa con TI. Y aunque ya hemos visto mucha transformación en la esfera industrial, también está claro que no se detendrá en el corto plazo.
Según reporte de Markets and Markets, para 2025, el mercado de IIoT tendrá un valor de $110,600 millones de dólares, y esto solo impulsará aún más las tendencias de digitalización que he visto hasta ahora.
Estas tendencias durante la próxima media década plantearán nuevas demandas y desafíos para la TI que respalda las infraestructuras industriales. El entorno de OT necesita cada vez más interactuar y conectarse con redes previamente segregadas. Los dispositivos IIoT entregan nuevos datos que deben procesarse, almacenarse y analizarse. Todo esto significa que la TI en los entornos de producción deberá ser lo suficientemente escalable y flexible para admitir los nuevos procesos y funcionalidades que se abren paso en la infraestructura.
Estas son las 6 tendencias de los próximos años que desempeñarán un papel importante en la forma en que la TI industrial deberá adaptarse.
1 – Convergencia de TI y OT
La convergencia de TI y TO sigue siendo la mayor fuerza impulsora para la transformación en TI Industrial. Las máquinas previamente modularizadas ahora están conectadas y los sensores de IoT están entregando datos sobre todos los aspectos de la producción.
Cada vez está más claro que un enfoque aislado, como era anteriormente, ya no es útil. Ahora hay muchas más interfaces y puntos de contacto entre varias áreas diferentes en la fabricación, en particular que antes, TI, OT y IIoT, y esto trae sus propios desafíos. ¿Cómo pueden los técnicos y administradores de sistemas asegurarse de que las interfaces estén funcionando? ¿La información fluye desde el piso de producción a los centros de datos o la Nube como debería? ¿Y cuál es la mejor manera de obtener una descripción general precisa de la imagen completa?
Todas estas son preguntas que los profesionales de la TI industrial deberán plantearse en los próximos años.
2 – La ciberseguridad como máxima prioridad
La pandemia ha provocado un aumento masivo de los ciberataques. Daniel Newman en Forbes afirma que sólo de enero a abril de 2020, hubo un aumento del 238% en los ataques a los bancos y un aumento del 600% en los ataques a los servidores en la Nube. Esto ayuda a resaltar cómo el crecimiento exponencial de los ciberataques continuará impulsando la tendencia de la ciberseguridad en todas las verticales, y eso incluye la fabricación.
Si bien la ciberseguridad no es nada nuevo para las TI en entornos industriales, la digitalización en la fabricación ha traído consigo sus propios desafíos únicos. Los sensores, dispositivos e implementaciones de IIoT generan riesgos de seguridad que ya han sido bien documentados. Mientras tanto, los componentes de OT deben «abrirse» para conectarse con nuevos sistemas y dispositivos, y esto proporciona un conjunto completamente diferente de riesgos de seguridad. El problema se agrava por el hecho de que los conceptos y herramientas de seguridad estándar que se desarrollaron para TI no funcionan necesariamente para OT.
Dicho todo esto: es posible conectar el mundo de OT, pero se requiere una estrategia sólida de ciberseguridad, y la TI de soporte deberá adaptarse para satisfacer las nuevas demandas de seguridad de OT para proteger los componentes y dispositivos de IIoT.
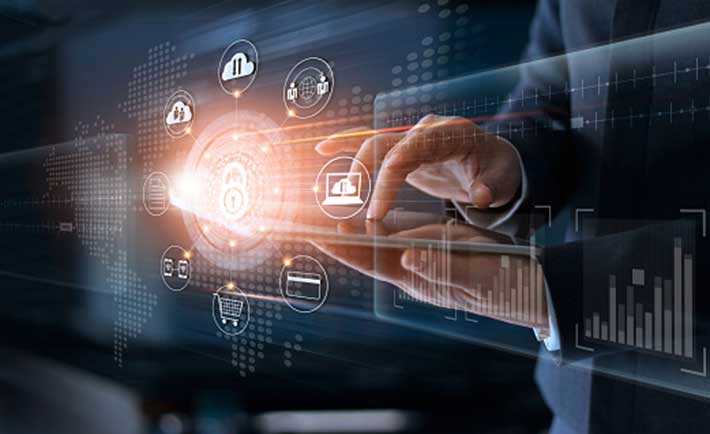
3 – La ventaja industrial
Teniendo en cuenta la importancia de los datos que provienen de la planta de producción y los dispositivos IIoT, las puertas de enlace industriales (o puertas de enlace inteligentes) han comenzado a desempeñar un papel fundamental en los entornos de fabricación.
Estos dispositivos se pueden conectar a varios elementos en la planta de la fábrica y son responsables de agregar datos y enviarlos a varios puntos finales. Esto significa que son las puertas de enlace, como su nombre indica, para acceder a datos importantes sobre el proceso de producción.
La integración de dispositivos en la infraestructura actual seguirá siendo un tema central para muchas empresas en su avance hacia la Industria 4.0. No solo eso, sino que garantizar que estas puertas de enlace estén conectadas, disponibles y funcionando como deberían, será parte de la tarea de monitorear la infraestructura general.
4 – Estandarización de protocolos de comunicación
Con la interconexión de los sensores y dispositivos de IoT con OT y otros puntos de contacto, existe la necesidad de un «lenguaje» común para garantizar que los componentes de las diferentes tecnologías se comuniquen. El estándar OPC UA está aumentando como una opción ampliamente adoptada, y se espera que esta tendencia continúe en los próximos años.
Pero cualquiera que sea el estándar que adopte un fabricante, será necesario implementarlo e integrarlo en la infraestructura existente.
5 – Soluciones de Nube flexibles
Hoy en día, el procesamiento crítico puede ocurrir en varios lugares: en la Nube, en las instalaciones, en el borde o incluso en una combinación de estos. La tendencia hacia la arquitectura de múltiples Nubes continuará, donde los servicios de múltiples Nubes se combinan en una solución. Otra tendencia es el uso de escenarios híbridos, donde los dispositivos de borde, el hardware local y los servicios en la Nube se combinan en una solución integrada.
Será importante para los fabricantes identificar sus requisitos y diseñar o seleccionar la mejor solución en la Nube en función de sus casos de uso específicos.
6 – Procesamiento y análisis de datos
La naturaleza del IIoT significa que los sensores, dispositivos y maquinaria conectada generan datos. Estos datos pueden ser extremadamente útiles para identificar tendencias, obtener información sobre el proceso de producción y tomar decisiones.
Solo a modo de ejemplo: recopilar información sobre el funcionamiento de una máquina mediante sensores puede darle pistas sobre cuándo será necesario mantenerla. Esto permite a los técnicos realizar un mantenimiento predictivo en lugar de mantener la máquina al por mayor según la fecha del calendario y, por lo tanto, ahorrar costos innecesarios. Sin embargo, es necesario recopilar esos datos, comprender la información que genera y, cuando sea necesario, enviar alarmas cuando los factores indiquen que la máquina necesita servicio, por ejemplo, cuando ciertos valores superan los umbrales definidos.
O tomemos la eficiencia energética como otro ejemplo: existe una creciente presión sobre los fabricantes para que aumenten la eficiencia energética a través de la legislación y las regulaciones. Usando datos de medidores de potencia (comunicados a través de protocolos como Modbus), los fabricantes pueden analizar su uso de energía e identificar formas de mejorar. Pero nuevamente, los datos deben recopilarse y entenderse primero.
El desafío es identificar qué datos se entregan y averiguar cómo usarlos. Esta comprensión también informará cómo se implementa el IIoT y, por lo tanto, es una parte crucial del rompecabezas.
Con todas las innovaciones y cambios que se están produciendo, la clave es tener la capacidad de adaptar la TI rápidamente y escalar en consecuencia a medida que los nuevos requisitos continúan moldeando la manufactura.
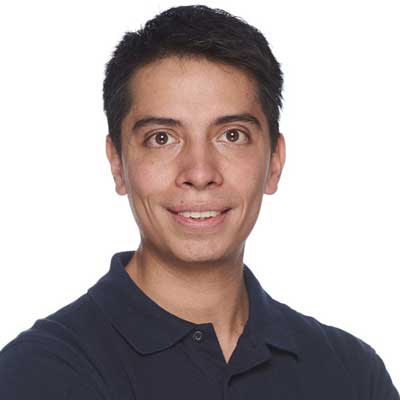
Por: David Montoya,
Director Regional,
Paessler América.